Salsa
Strain imager for engineering applications
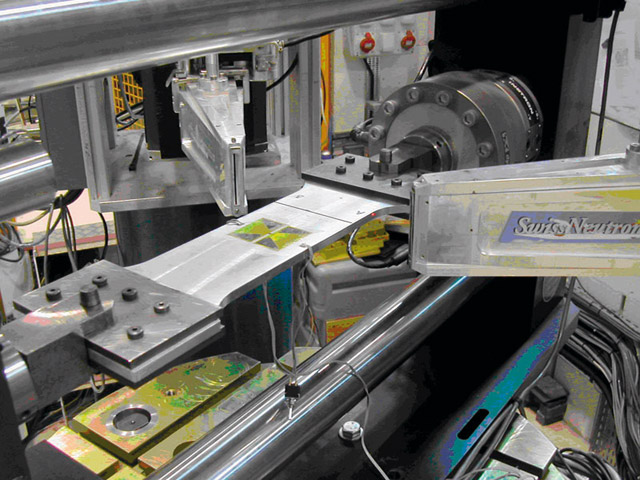
Experimental set-up at SALSA for measurement of the stress in a welded plate under fatigue crack growth.Measurements:a) in the transverse direction ; b) in the longitudinal direction.
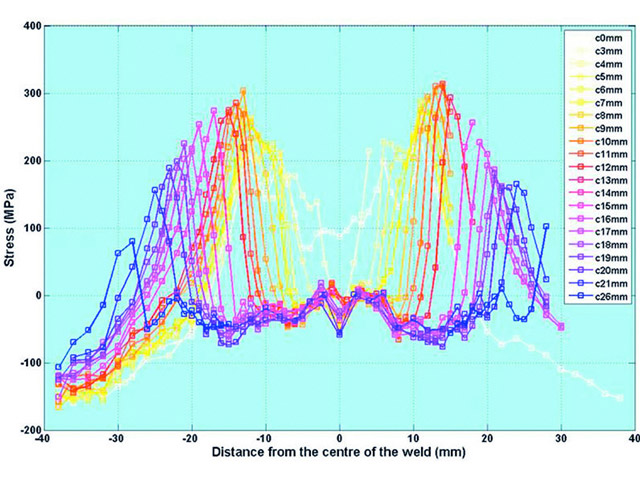
Measured evolution of the residual stresses with fatigue crack growth.
Residual stress and fatigue crack growth
The availability of the 50 kN in-situ stress rig allows investigation of the dynamics of fatigue crack growth. These studies have important implications for component life predictions, particularly in the safety-critical aerospace industry.
A recent experiment attempted to understand why fatigue behaviour seen experimentally does not correspond to that predicted by linear elastic fracture mechanics. The 50 kN test machine, weighing approximately 250 kg, was mounted on the hexapod (fig. 1). An aluminium 2024 alloy MIG welded specimen was used as a test piece.
Crack growth was performed by cyclic fatiguing at PMAX = 34 kN. In total the weld was subjected to over 100,000 fatigue cycles. Fig. 2 shows the variation of residual stress in the weld with crack length c. The results show that in fact linear elastic fracture mechanics are valid for the assessment of fatigue performance and that previous innacuracies were due to incomplete knowledge of the initial residual stress state.
Ref.: CDM Liljedahl and O. Zanellato